南阳数控仿型铣定制
数控仿型铣的工作原理是通过计算机数控系统(CNC)控制机床的运动和加工过程。首先,将需要加工的零件的三维模型输入到计算机数控系统中,然后根据模型生成相应的加工程序。加工程序中包含了机床的加工路径、加工参数等信息。接着,计算机数控系统将加工程序传输到机床的控制系统中,控制系统根据加工程序控制机床的运动和加工过程。数控仿型铣在加工过程中,计算机数控系统还会实时监测机床的运动状态和加工状态,确保加工过程的稳定性和精度。数控仿型铣的故障排除和维修技巧。南阳数控仿型铣定制
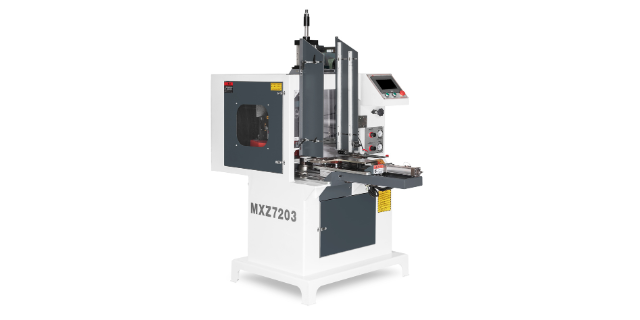
数控仿型铣的基本原理是通过计算机程序控制铣床进行加工,实现复杂形状的加工。其工作原理如下:设计CAD图纸首先,需要使用计算机辅助设计(CAD)软件设计出需要加工的零件的三维模型。在CAD软件中,可以对零件进行各种操作,如旋转、平移、缩放等,以得到所需的形状。编写CAM程序接下来,需要使用计算机辅助制造(CAM)软件编写加工程序。CAM软件可以将CAD图纸转换为机床可以理解的代码,以便机床能够按照程序进行加工。在编写CAM程序时,需要考虑加工路径、切削参数、刀具选择等因素。加工:z后,将CAM程序上传到数控铣床上,启动加工过程。数控铣床会按照程序进行加工,直到完成所需的零件。德宏双工位数控仿型铣电话数控仿型铣的未来发展方向。
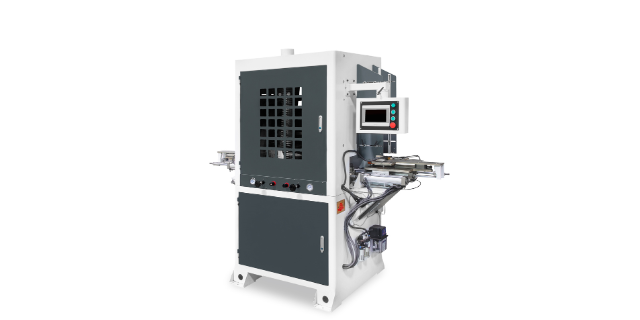
数控仿型铣是一种高精度的机床,用于加工各种金属和非金属材料。为了确保机床的正常运行和延长其使用寿命,需要进行定期的维护和保养。以下是一些常见的维护和保养建议:定期校准机床:机床的精度和稳定性是其重要的性能指标之一。为了确保机床的精度和稳定性,应定期进行校准和调整。校准和调整的方法和标准应根据机床的具体情况而定。定期备份机床程序和数据:数控仿型铣通常使用计算机控制系统,程序和数据是机床正常运行的关键。为了避免程序和数据的丢失或损坏,应定期进行备份和存储。定期培训机床操作人员:机床操作人员是机床正常运行的关键。为了确保机床的正常运行和延长其使用寿命,应定期进行培训和教育,提高操作人员的技能和水平。
全自动数控仿型铣是一种高精度、高效率的机械加工设备,普遍应用于汽车、航空、航天、电子、模具等行业。它的主要作用是通过数控技术,将设计图纸中的三维模型转化为机床上的加工程序,实现对工件的高精度加工。全自动数控仿型铣的应用主要体现在以下几个方面:1.汽车制造在汽车制造中,全自动数控仿型铣主要用于制造汽车零部件,如发动机缸体、缸盖、曲轴、凸轮轴等。这些零部件的加工精度要求非常高,而全自动数控仿型铣可以通过数控技术实现高精度加工,提高了汽车零部件的质量和性能。2.航空航天制造在航空航天制造中,全自动数控仿型铣主要用于制造飞机零部件,如机身、机翼、发动机等。这些零部件的加工精度和表面质量要求非常高,而全自动数控仿型铣可以通过数控技术实现高精度加工和高质量表面处理,提高了飞机零部件的质量和性能。恒定加工余量是在数控仿形铣中实现稳定的高生产率的基本准则之一。
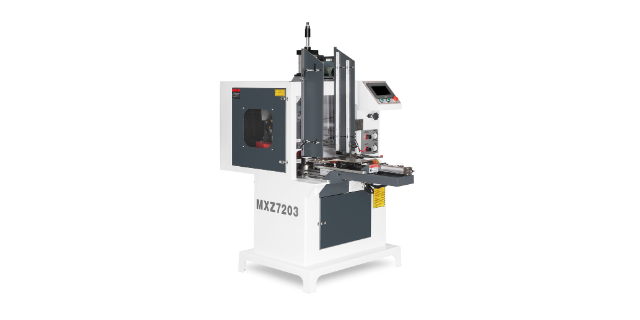
数控仿型铣是一种利用数控技术实现的铣削加工方式,其主要特点是通过数控系统控制铣床进行自动化加工,实现对复杂曲面的高精度加工。数控仿型铣的出现,极大地提高了加工效率和加工精度,同时也降低了生产成本,成为现代制造业中不可或缺的一部分。数控仿型铣的原理。数控仿型铣的工作原理是将物体的三维模型输入到数控系统中,通过数学算法将模型转化为铣削路径,然后控制铣床进行自动化加工。具体来说,数控仿型铣的加工过程可以分为以下几个步骤:制作物体的三维模型:首先需要制作物体的三维模型,可以使用计算机辅助设计(CAD)软件进行制作。转化为铣削路径:将三维模型输入到数控系统中,通过数学算法将模型转化为铣削路径,即将物体的三维形状转化为铣削刀具的运动轨迹。编写加工程序:根据铣削路径编写加工程序,包括刀具的选择、切削参数的设置等。加工过程:将加工程序输入到数控系统中,控制铣床进行自动化加工。检验加工结果:加工完成后,需要对加工结果进行检验,以确保加工精度和质量。随着科技的不断进步和制造业的发展,数控仿型铣在工业生产中扮演着越来越重要的角色。临沧数控仿型铣哪家好
数控仿型铣工作前请确认每支主轴转向。南阳数控仿型铣定制
数控仿型铣可以对模具进行高精度加工。模具是制造工业中的重要工具,其精度和质量对产品的影响至关重要。数控仿型铣可以通过高精度的加工方式和先进的数控技术,实现对模具的高精度加工。它可以通过编程控制刀具的移动路径和参数,以精确复制和模仿复杂的轮廓和形状,从而保证了模具的精度和质量。此外,数控仿型铣还可以通过自动化加工和智能化的加工策略,进一步提高模具加工的效率和一致性。因此,数控仿型铣在模具加工领域具有广泛的应用前景。南阳数控仿型铣定制